Step 2. - Combing
Combing, also known as hackling, is carried out by the scutcher or the spinner.

The fiber has any impurities removed, it is separated and laid parallel, graded, and stretched out into slivers, soft and glossy continuous ribbons.
Step 3. - Preparation For Spinning
During preparation, slivers of combed flax are mixed together, blending several batches of fibers originating from different fields, regions, and years.
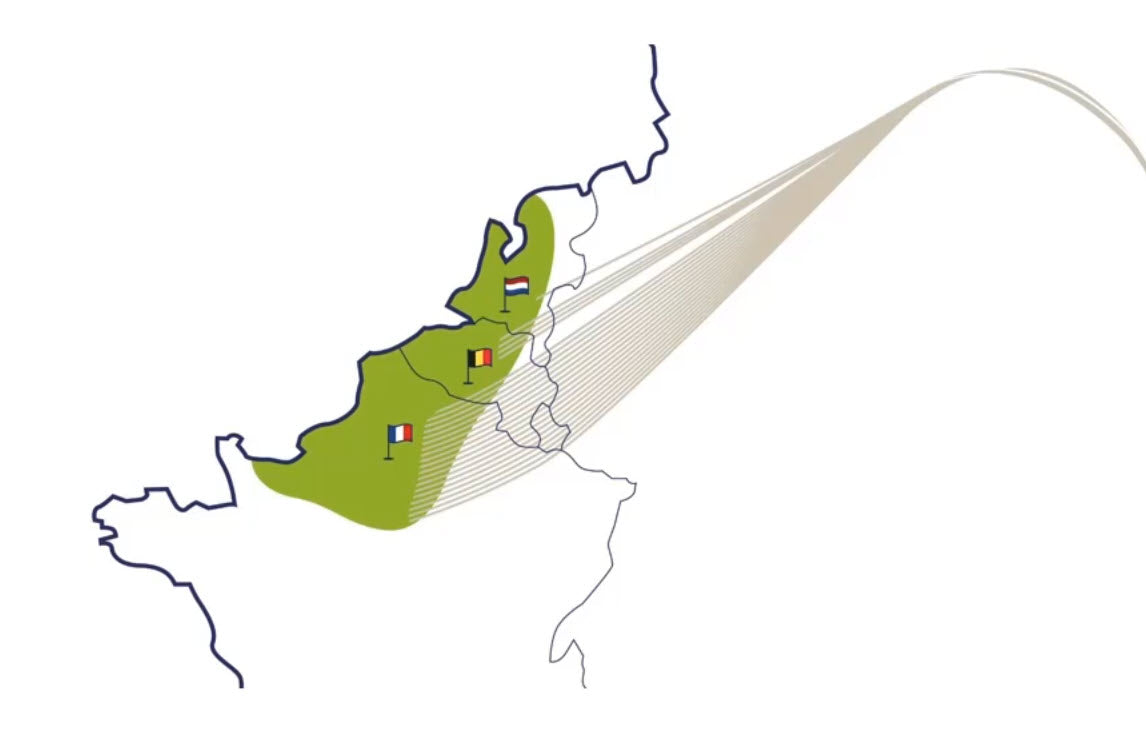
This unique expertise, comparable to the methods used for champagne and cognac, allows the qualities of each batch to be combined to ensure high quality and consistency.
The higher the required yarn quality, the higher the number of batches: a requirement that in recent years has led to extreme mixtures, with up to 32 different batches!
Mixed together, equalized, and stretched out, the slivers become roving before being spun.

The European spinning industry handles fibers with care, refining them exclusively by a mechanical process in order to preserve their structure and qualities.
Step 4. - Spinning
The techniques vary depending on the type of yarn that is being produced:
-
Fine yarns destined for clothing, home linens, etc., re-obtained through “wet” spinning with immersion in water heated to 60°C. This soaking facilitates the smooth separation of the fibers and allows for a great fineness to be achieved.
-
More rustic and thicker yarns, for decoration, rope, etc., are produced by “dry” spinning.
For example:
- Nm 2.6 for upholstery fabrics,
- Nm 26 for average shirting fabric,
- Nm 39 for upmarket shirting or fine jersey, and up to Nm 50 or 70 for exceptional qualities.
As for bleaching, the European spinning industries comply with the strictest environmental rules and favor peroxide-based rather than chlorine-based agents.
Step 5. - Weaving
Linen has freed itself from the vagaries of trends to become synonymous with innovation.
It includes classic fabrics, twills (like denim), herringbone; more sophisticated satins and crêpes; jacquards that accommodate designs woven in color or monochrome (damask); terrycloth and velvet, along with more unexpected possibilities.
A fabric is the result of the crisscrossing of warp yarns (running in the direction of the fabric’s length) and weft yarns (running crossways, its measurement equaling the fabric’s width). The rhythms this intertwining undergoes – weaves – create the fabric’s pattern and texture.
The exceptionally broad range of possibilities, combined with the choice of thicknesses and thread effects make it possible to develop a multiplicity of creative fabrics for fashion, home linens, decoration, and so on.
Step 6. - Knitting
Knitting brings suppleness, elasticity and a wrinkle-free added value to linen.

Linen’s naturalness, solidity, thermoregulation, moisture absorption, and softness, along with being hypoallergenic and antibacterial, making it a choice fiber for knits.
Thanks to the innovations of European spinners, linen can be knitted in various ways.
Knit fabric or “jersey” is knitted on circular machines, then cut-and-sew assembled for collections of T-shirts, tops, sweatshirts, etc.
Knitwear, on the other hand, is produced on flatbed knitting machines in set forms, ready to be assembled, or in 3D without seams.
Step 7. - Finishing
Linen fabrics lend themselves to all kinds of finishing's.
Boasting an excellent ability to take color and perfectly suited to low environmental impact dyes, linen fabrics can be equally well printed with offset or screens as it does new digital processes and takes metallic coatings for a ‘glitter’ effect.

Linen lends itself to any decorative finishes, it can
be embroidered, burnt out, needle punched, etc.
On the technical side, various treatments add and increase linen fabrics’ performance capabilities, for example, anti-shrinkage, wrinkle-proofing, stain resistance, or waterproofing for fashion and outdoor decoration.
Washed linen is obtained through one or a combination of finishing technologies. Mechanical processes involve warm air flow or stonewash. Wet processes use softeners or enzymes during washing.
The result offers a cozy and soft handle and a supple texture that doesn't require ironing.